(Excerpt from
the upcoming book on Robert Slass, Founder of Rotor Clip Company, a successful
US manufacturer of retaining rings)
In September 1957 Bob Slass opened a small company on Allen Boulevard in Farmingdale, New York, with the intent of making retaining rings. He called his company “RotorClip.”
The company consisted
of one, 2,000 square foot building, but that didn’t discourage the young
entrepreneur. He knew that he was not only starting a business, but establishing
a career whose skills and talents he would call upon to make Rotor Clip the
successful company it would someday become.
As
manufacturing lost its dominant place in our society, it was easy to find fault
with it. Factory jobs were dirty, boring and uninspiring. The work was back
breaking and you didn’t use your mind. Many people (especially young people)
concluded that a factory wasn’t the place to pursue a challenging career.
But
innovation and ingenuity were always a part of factory work as Bob demonstrated
during the early days of Rotor Clip. For example, he used his knowledge of tools
and engineering to refurbish machines and make them productive with very little
investment.
![]() |
PLC's played a key role in one of Rotor Clip's most important
innovations: Rings on Wire.
|
Instead of
purchasing new plating equipment, he modified empty paint cans and placed them on
a cam mechanism he designed and built to mechanically plate rings for corrosion
protection.
Bob experimented
with stamping “rings within rings” as a way to reduce scrap and get the most
efficient yield from a strip of steel. These experiments led to Bob’s design of
several generations of progressive dies, concepts that would revolutionize retaining
ring production and eventually become his signature work.
Today, manufacturers
like Rotor Clip have seen these roles evolve into more complex, technology-based
careers like those involving Electrical Design/PLC.
![]() |
Programmable Logic Controllers (PLC) play a key role
in many systems and machines like this security control system.
|
PLC’s or
Programmable Logic Controllers are digital computers used for automation of
industrial electromechanical processes. They range from assembly lines, to
amusement rides, to light fixtures. PLC’s are used in severe environmental conditions,
(for example dust, moisture, heat, or cold), as opposed to a normal computer
that wouldn’t work in these conditions. (http://en.wikipedia.org/wiki/Programmable_logic_controller).
PLC systems
are inside many things in Rotor Clip’s plant, from security systems to machines
used to package retaining rings (See “rings on wire” picture). Machine
automation is the future and Rotor Clip relies on Electrical Design Engineers to
utilize PLC systems to design and troubleshoot new equipment.
When they speak
of the “skills gap” in manufacturing, they are eluding to the lack of qualifications
needed for many of today’s factory jobs. This is due to the failure of young
people to see factory work as technology driven requiring more than the ability
to turn a machine on and off. But there has been a positive trend recently as educational
institutions and corporations partner to provide the skills factories need
(like Electrical designers) to improve and thrive in today’s competitive global
world.
Joe Cappello
is Director of Global Marketing for Rotor Clip Company. If you would like to
continue to receive excerpts from his upcoming book on Rotor Clip and American
manufacturing, click here and e-mail him your request. He'll
add you to his mailing list for updates.
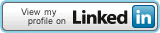
No comments:
Post a Comment